Throughout history, both at home and abroad, the iterative updates of material handling technology have marked innovation and technological progress. Traditional hydraulic forklift handling can no longer meet the development needs of today's social productivity. Both industrial and commercial environments require innovative products to meet the development of the new era, and with the development of artificial intelligence and big data, AGV and AMR have emerged.
Although AGV (automated guided vehicle) and AMR (Autonomous Mobile Robot) both move materials from one place to another, their similarities stop here.
Fixed route vs. intelligent navigation
AGV has the least in car intelligent functions and can only follow simple programming instructions. For navigation, it needs to be guided by wires, magnetic strips, or sensors, which typically require extensive and expensive facility updates to be installed, during which production may be interrupted. AGV is limited to following these fixed routes, and if changes are needed in the future, additional costs and production interruptions will be required. AGV can detect obstacles ahead, but cannot bypass them, so it can only stop on the track until the obstacles are removed.
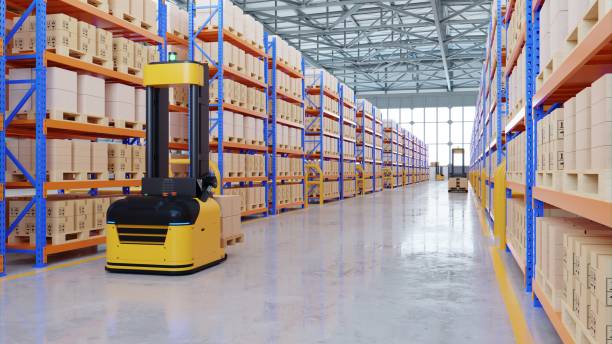
In contrast, AMR navigates through maps built on-site through its software or through pre loaded facility drawings. AMR uses data from cameras, built-in sensors, laser scanners, and complex software to detect the surrounding environment and choose the most effective route to reach the target. It works completely autonomously, and if there are forklifts, pallets, personnel, or other obstacles ahead, AMR will use the best alternative route to safely bypass them.
Expensive and cost-effective
Although AMR includes much more advanced technology than AGV, it is a cheaper solution. AMR does not require wires, magnetic strips, or other expensive modifications to building infrastructure, making it faster, cheaper to start and run, and does not cause costly interruptions to the production process. Due to the fast and easy deployment of AMR, they can almost immediately improve efficiency. With low initial costs and rapid process optimization, they provide very fast investment returns - typically less than six months. As the business grows, the implementation of AMR can be simultaneously expanded with minimal additional costs.
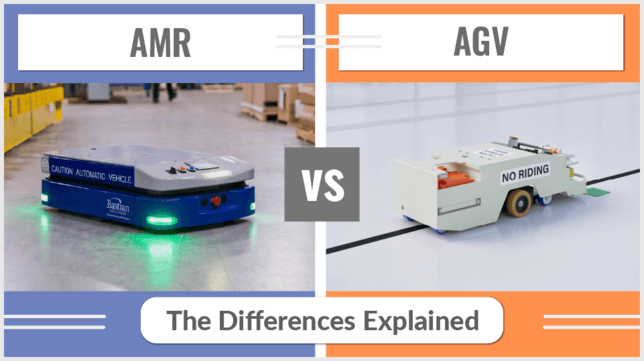
Flexibility and Security
AMR systems are usually more flexible than AGVs because they can be programmed to perform various tasks, including route planning, task management, and transportation. On the other hand, AGVs are usually designed for specific tasks, and without significant modifications, they may not be able to perform other functions.
Both AMR and AGV systems have safety functions, such as obstacle detection and emergency stop buttons, but AMR's excellent anti-collision sensor system and backend scheduling system often have broader safety functions.
Modern manufacturing environments can no longer rely on expensive and inflexible legacy technologies. They also cannot afford to continue unproductive manual transportation of materials, especially in today's tight labor market. Autonomous mobile robots outperform AGVs in terms of flexibility, cost-effectiveness, investment return, and productivity optimization.